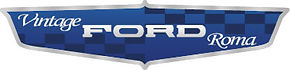
VINTAGE FORD ROMA
1910 - 1927
Il trasferimento ad Highland Park e la nascita del modello organizzativo fordista
La continua e crescente domanda di Model T impone all’inizio del 1910 il trasferimento dal 411 di Piquette Avenue ad Highland Park dove sorge il nuovo ed avveniristico sito produttivo interamente realizzato in acciaio e cemento armato, progettato dal tedesco Albert Kahn.
Gli spazi a disposizione sono ora quasi quadruplicati ed è effettuato un ulteriore quanto definitivo perfezionamento del metodo produttivo con l’introduzione nell’ottobre del 1913 della catena di montaggio.

La catena di montaggio rappresenta l’attuazione pratica dei principi esposti ad inizio secolo da Frederick Wislow Taylor nella sua teoria relativa all’Organizzazione Scientifica del Lavoro.
La struttura organizzativa taylorista è nel suo insieme caratterizzata da una marcata rigidità strutturale in base alla quale sono definiti compiti e funzioni. Traendo chiara ispirazione dal modello militare decisioni, controllo e flusso informativo si muovono a senso unico solamente dall’alto verso il basso, percorrendo quindi l’ipotetica piramide che da forma al sistema organizzativo nella sola via che si muove dal vertice alla base.
Se fino a pochi anni prima l’automobile era stata costruita servendosi di un’unica postazione verso la quale erano fatti convergere tutti i componenti ora è la vettura ad andare gradualmente incontro a tutte le parti che la compongono avvalendosi dell’articolato sistema di ganci e carrelli che compone la catena di montaggio.





L’assemblaggio è infatti scandito in maniera costante e continua da più fasi tra loro complementari: completato il telaio e montata tutta la meccanica si procede con l’assemblaggio di carrozzeria ed interni.
Ogni scocca è infatti progressivamente movimentata sulla linea produttiva di appartenenza e, senza mai muoversi da questa, è direttamente condotta innanzi agli operai che agiscono sulla base di quanto stabilito nella scheda di lavorazione.
L’operaio rimane quindi l’effettivo esecutore del processo produttivo, il cui compito è svolgere tutte quelle operazioni fortemente standardizzate e ripetitive che sono imposte dalla stessa movimentazione della catena di montaggio.
Gli incessanti ritmi a cui è sottoposto il lavoratore della catena di montaggio sono magistralmente descritti in chiave comica dal grande Charlie Chaplin nel film Tempi Moderni del 1936: celebre è infatti la scena in cui il malcapitato Charlot appare letteralmente soggiogato dal nastro trasportatore e dalla persistente ripetitività delle operazioni di cui si compone il suo lavoro.
Data la palese rigidità strutturale che pervade l’intero sistema il ciclo produttivo è svolto da più reparti ognuno dei quali rappresenta una vera e propria unità che, dotata di una propria autonomia organizzativa ed operativa, è chiamata a compiere la fase di propria competenza sotto la supervisione di un responsabile al quale è assegnata la qualifica di capo reparto.
Il capo reparto, soggetto dotato di una specifica preparazione tecnica, oltre ad essere unica figura di raccordo tra il vertice e la base della piramide organizzativa, risulta di fondamentale importanza ai fini dell’attuazione del learning by doing, strumento organizzativo finalizzato all’ottimizzazione del fattore lavoro e basato sullo scambio di conoscenza pratica.

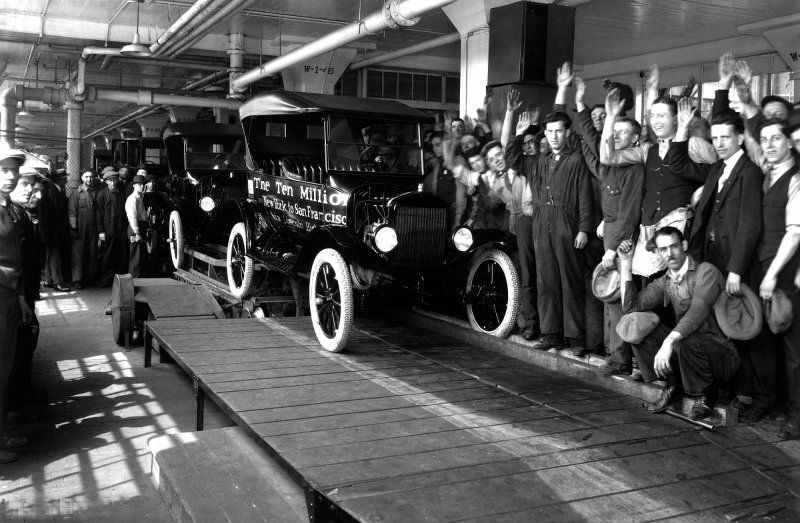


Se il lavoratore è infatti selezionato ed addestrato all’utilizzo del macchinario solo ed esclusivamente sulla base delle operazioni standard che sarà chiamato a compiere, il problema causato dal manifestarsi di un evento che non risulta ricompreso nello standard previsto sarà superato mediante l’intervento del capo reparto che proprio in quel momento, dopo aver bloccato la catena di montaggio, fornirà all’operaio le nozioni necessarie per la risoluzione dell’imprevisto.
La procedura appena descritta proprio perché finalizzata allo scambio di conoscenza pratica è di fatto l’unica causa contemplata ed idonea al temporaneo fermo tecnico della catena di montaggio.
Per quel che concerne gli aspetti retributivi Henry Ford decide prima di raddoppiare la paga base, che sale a cinque dollari al giorno, e poi di fissare la durata della giornata lavorativa in otto ore.
Dopo poco tempo trova attuazione il sistema a cottimo differenziale, idoneo a garantire una retribuzione del fattore lavoro proporzionata alla quantità di lavoro svolta e di consentire, secondo lo stesso Henry, all’operaio l’acquisto del prodotto finale per cui ha prestato il proprio lavoro.
Al fine di massimizzare ulteriormente i rendimenti la Ford Motor Company introduce anche uno specifico sistema sanitario e di prevenzione degli infortuni definito sulla base del livello di inquadramento di ciascun dipendente e finalizzato alla minimizzazione dei costi sanitari del personale.
Da un punto di vista prettamente operativo nello stabilimento di Higland Park l’assemblaggio di un telaio Model T diviene possibile in un ora e trentatre minuti, con il lavoro di nove operai ad un costo industriale unitario pari a 93 dollari.
A tale riduzione dei tempi e dei costi corrisponde un drastico quanto inevitabile taglio riguardante gamma di colori e finiture. Il rosso, il verde, il grigio ed il perla sono definitivamente abbandonati in favore del nero, l’unico smalto di fabbricazione giapponese che, spruzzato a bassa pressione, risulta avere tempi di asciugatura compatibili con il ritmo produttivo di Highland Park. Tutti i particolari in ottone sono proposti in acciaio verniciato, materiale previsto anche per il cruscotto dove va a sostituire il legno di ciliegio.

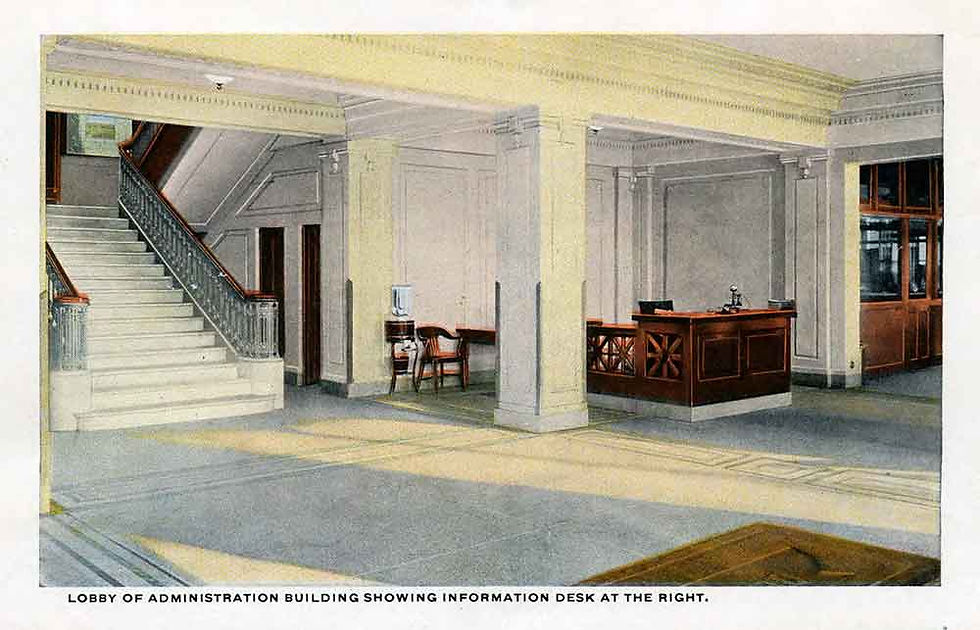


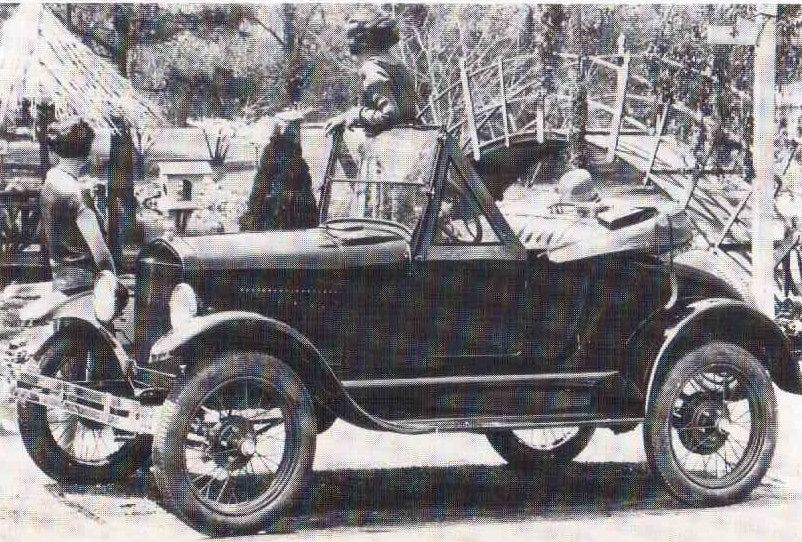


quindicimilionesima vettura prodotta dalla Ford
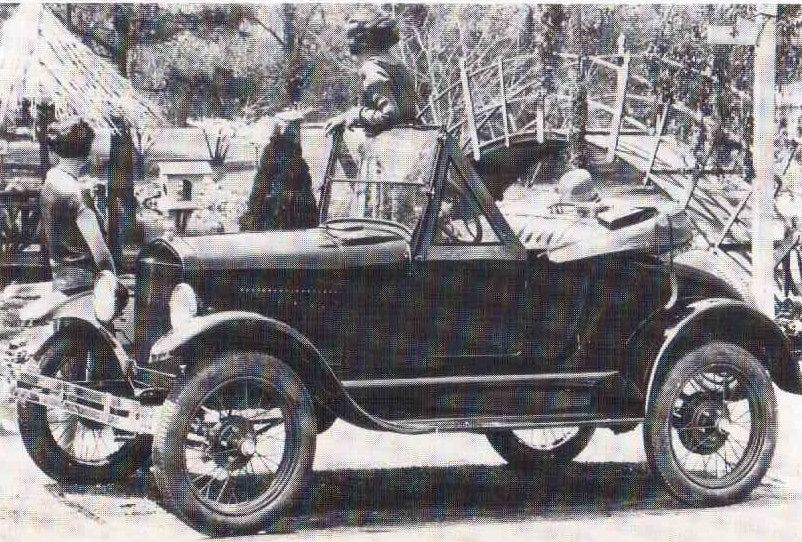
Se già nel 1912 un terzo delle vetture vendute sul mercato statunitense era una Ford col crescere della produzione il Model T diventa a tutti gli effetti un vero best-seller, la concorrenza è letteralmente azzerata anche grazie a prezzi fortemente competitivi che consentiranno di varcare nel 1923 la soglia dei due milioni di esemplari prodotti.
Al raggiungimento di questo risultato segue la prima quanto inevitabile flessione delle vendite, l’interesse del mercato statunitense è fortemente attratto dai marchi emergenti tra i quali spiccano Chevrolette e General Motors.
Dopo aver tramutato oltre quindici milioni di persone in automobilisti Tin Lizzie, questo il simpatico soprannome coniato oltre oceano per la Model T, questa esce di produzione nel 1927 per raggiunti limiti di età.
Il Modello Fordista, giustamente criticato per i suoi palesi limiti nella gestione delle risorse umane, rimarrà a lungo il paradigma produttivo di riferimento di tutto il secolo, trovando nuova vita negli anni cinquanta quando, opportunamente rivisitato, sarà adottato da Toyota e Fiat, contribuendo in tal modo al grande boom economico italiano di cui la nostra Fiat 600 rimane ad oggi indiscutibile icona automobilistica.